About the Customer
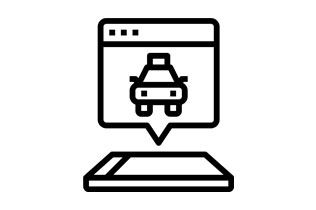
Our Customer is a Japanese car manufacturing giant, is one of the world’s leading auto manufactures.
Problem Statement
- Quality management in any manufacturing industry plays a vital role to establish the conformity of quality at Pre-production, In-line Production, and pre-shipment inspection stages. The customer was using manual quality inspection, resulted into rework, re-ordering, long delays, financial loss due to high-quality variance and rejections.
- Due to manual works, information, and data stored in silos and customer was struggling to make any objective analysis such as root cause, financial impact assessments.
- Various applications and modules were available as dis-integrated solutions and the quality module was not integrated with other modules developed.
Solutions Delivered
- The quality management is digitised from quality inspection to quality control through quality assurance for total quality management and digital quality system in the plant
- The quality management system was developed to collect data at all three stages viz pre-production, in-line production and pre-shipment to measure any deviations and conformity of process and product and make the end product defects-free.
- Quality workers to quality inspectors at every stage of checking, measuring is empowered with Windows 10 tablet to enter data that can be directly evaluated with quality master
- Developed N Tier Architecture for the development of quality modules.
- Tools and technologies used: UWP, SQL 2012, VS 2017, MVC 4, and Microsoft Azure.
- Integrated Queued Hosted service for uploading a larger volume of data in the background without affecting the performance.
- Web API’s used for data transmission.
- Used MVC for front-end and UWP for Tab application.
- JSON was used to store temporary data in Tab.